Table of Contents
Indigo Dyes
Indigo dyes are widely used dyestuff of all time in the denim coloration process. However, indigo dyes are the common choice of the denim manufacturer for their extremely wash fastness properties. However, during the 13th century, Marco Polo saw indigo being prepared in China. Historically, this dye was used many centuries before the Christian era in the Far East.
Denim
Denim or jeans products are commonly used in modern times. However, it is the oldest, most widely used, most fashionable, and most versatile fabric in the world. Basically, these products have a great demand from the young generation as well as other people.
Denim Dyeing Process
There are four denim dyeing processes with Indigo for denim dyeing. They are-
- Rope/ Ball warp/ Chain dyeing
- Slasher/ Open warp/ Sheet dyeing
- Loop dyeing
- Beam dyeing
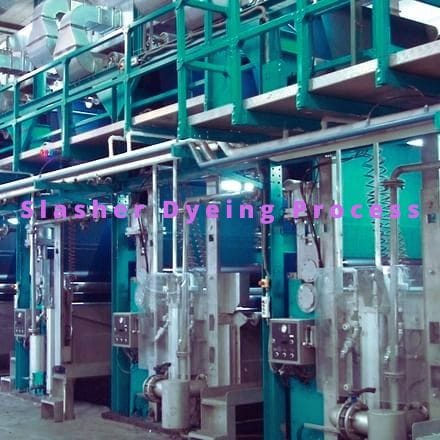
Slasher Dyeing Process of Denim With Indigo Dyes
The slasher dyeing dyes the yarns in the warp beam form. Basically, it is a continuous process that combines dyeing and sizing in a single operation. Dyeing is consequently done by continuously passing warp yarns through several (at least 5) troughs of indigo dye liquor. The dyed yarns are then sized and wound onto a warp beam to be ready for use in the next weaving process. The slasher dyeing is usually of inferior quality as compared to rope dyeing shade evenness or side-to-side shade variations. Moreover, in slasher dyeing, the penetration of dyestuff is poorer, and it easily reveals an uneven pick-up along its width with the distortion of the pad roll.
Characteristics of the Slasher Dyeing Process
The following are the characteristics of the slasher dyeing process. They are-
- Firstly, as each yarn is independently subjected to treatment it requires less time. It needs 6-10 dye baths per vat.
- Secondly, warp yarns are supplied from warp beams. Most of the machine’s capacity is 9500 warp yarns having 300-750 warp yarns per beam.
- After that, the number of total warp yarns is determined by yarn count and denim fabric design.
- Lastly, the yarn count which is used in this process ranges from 1-30 Ne.
Flow Chart of Slasher Dyeing and Sizing:
The following is the flow chart of the slasher dyeing and sizing process. They are-
Warper’s Beam
↓
Pretreatment (Scouring) bath
↓
Dryer- wash bath (1, 2, 3)
↓
Color box – 1
↓
Dryer – 1
↓
Color box- 2
↓
Dryer – 2 (Air oxidation is done here)
↓
Color box – 3
↓
Steam box
↓
Color box – 4
↓
Yarn pass between a set of guide roller for oxidation
↓
Color box – 5
↓
Oxidation
↓
Color box – 6
↓
Guide Roller
↓
Color box – 7
↓
Oxidation
↓
Color box – 8
↓
Oxidation
↓
Wash boxes (1, 2, 3)
↓
Dryer
↓
Sizing box
↓
Dryer
↓
Accumulator
↓
Leasing
↓
Winding
↓
Weaver’s beam
Advantages of the Slasher Dyeing Process
The following are the advantages of the slasher dyeing process. They are
- Firstly, it needs less space because of its compact design.
- Secondly, it needs less Oxidation and immersion times.
- Thirdly, it facilities a continuous dyeing process.
- After that, it has the flexibility to color change.
- Lastly, it requires less production cost.
Disadvantages of the Slasher Dyeing Process
The following are the disadvantages of the slasher dyeing process. They are
- Possibility of cross-shade variation
- Possibility of yarn rupture
- Productivity and flexibility in production are low
- Extra time is needed for a lot of change
- No versatility in denim production
- Reducing agent consumption is high
Features of Beam Creel Section:
The following are the features of the beam creel section. They are-
- Type- Sliding creel
- Arrangement- Two creels are placed parallel to each other.
- Creel capacity-16 warp beams can be placed in each creel.
- An electronic motor is available to slide the creel as well as mount the beams.
Sizing BATH and Sizing parameter:
The following parameter is required to maintain during size preparation in the size bath. They are–
- The capacity of the cooking tank
- Cooking Temperature
- Cooking time
- Pick up%
- Cylinder temperature
- Squeezing Pressure
- Delivery squeeze pressure: Lowest and Highest
- Stretch
- Refractro reading
- Viscosity
- Sizing Temperature
In sum, the slasher dyeing process is one of the best choices for dyeing specialists.