Table of Contents
What is combing process?
The combing process is essential to remove short fiber by combing action of the comb machine, which is not good for making finer yarn. In spinning technology, combing is considered an additional process. If we want to produce finer yarn, then we need to pass the combing process. Hence, combed yarn is produced in this method. After carding process, combing is done simultaneously to make combed yarn. The combing process is done to upgrade the quality of the raw materials. The comber does combing.
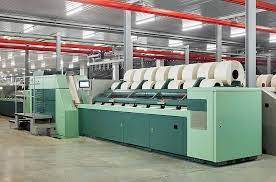
Image Source: rieter
Objectives of Combing Process
After carding action, combing is done to produce finer yarn or high-count yarn in the English counting system. The following objectives are achieved by the combing process:
- Firstly, remove short fibers before a pre-selected length.
- Secondly, fiber parallelization is improved by the combing action.
- After that, various types of foreign materials and impurities are removed by the combing action.
- Lastly, neps are eliminated by the combing action.
Contribution of Combing In Ring Spinning
Combing action improves different types of fiber properties as well as yarn quality. Followings are the contribution of combing. They are-
- The spinning value (count of yarn) is improved by the combing action.
- Yarn strength is improved by combing.
- Combing reduces the hairiness of the yarn.
- It accelerates the next process.
- Combing reduces imperfections like- neps, thick and thin places of the yarn.
- Better twist distribution is achieved by the combing action.
- Cleaner yarn is achieved by the combing process.
- It improves the smoothness of the yarn.
- Lustrous yarn is achieved by the combing process.
Combed yarn is generally used to produce knitted and woven fabrics. However, the fineness of the fabric depends on the properties of the yarn. Better quality yarn can give better knitting or weaving efficiency. Most importantly, the yarn should have evenness, regular in diameter and CV% should be low and the quality ratio should be high.
Yarn properties also affect the dyeing efficiency. So, the yarn should be free from different types of yarn faults.
2 comments
Chunna Ram
Good
mdAbdul mannan
Excellent