Table of Contents
Yarn Making
Yarn making is the process of turning common strands into yarn. it is as ancient as civilization itself, however indeed after all this time, it’s still a energetic, ever-evolving exchange that keeps material industry specialists interested and included. From choosing the perfect fiber to turning and passing on it into energetically colored strings, the preparation is an orchestra of imaginativeness, science, and ability. Here, we’ll find the puzzles of both modern engineered strands like acrylic and nylon and classic normal filaments like fleece, cotton, and silk. Each one of them has unmistakable qualities that determine how it is utilized in the tremendous cluster of merchandise made from yarn.
Advanced turning forms are utilized as we continue. It is apparent how old-world traditions and state-of-the-art gear combine to make the move from lightening to stringing. Our teacher instructs us about the approximate complexities of the yarn making process while serving as a specialized guide.
Machine Flow Chart of Cotton Yarn Making Process
Cotton fiber is widely used for yarn making. The yarn making process involves several key steps, from the initial raw materials to the final product. Here, I have presented the steps of the cotton yarn making process.
Fiber Selection
↓
Bale Opener
↓
Mixing
↓
Blow Room
↓
Carding
↓
Drawing
↓
Combing
↓
Simplex (Roving)
↓
Spinning (Ring Frame)
↓
Twisting
↓
Plying
↓
Winding (Autoconer)
↓
Finishing
Fiber Selection
Whereas correct specifics may contrast based on the kind of fiber and the planning utilize of the yarn, these common rules hold genuine for both normal and manufactured yarns. Each organize of the yarn-making prepare, which combines old-world craftsmanship and cutting-edge innovation, is imperative to the conclusion product’s quality and properties. The prepare begins with selecting the crude materials, which are more often than not strands such as cotton, fleece, flax, silk, or manufactured filaments like polyester and nylon.
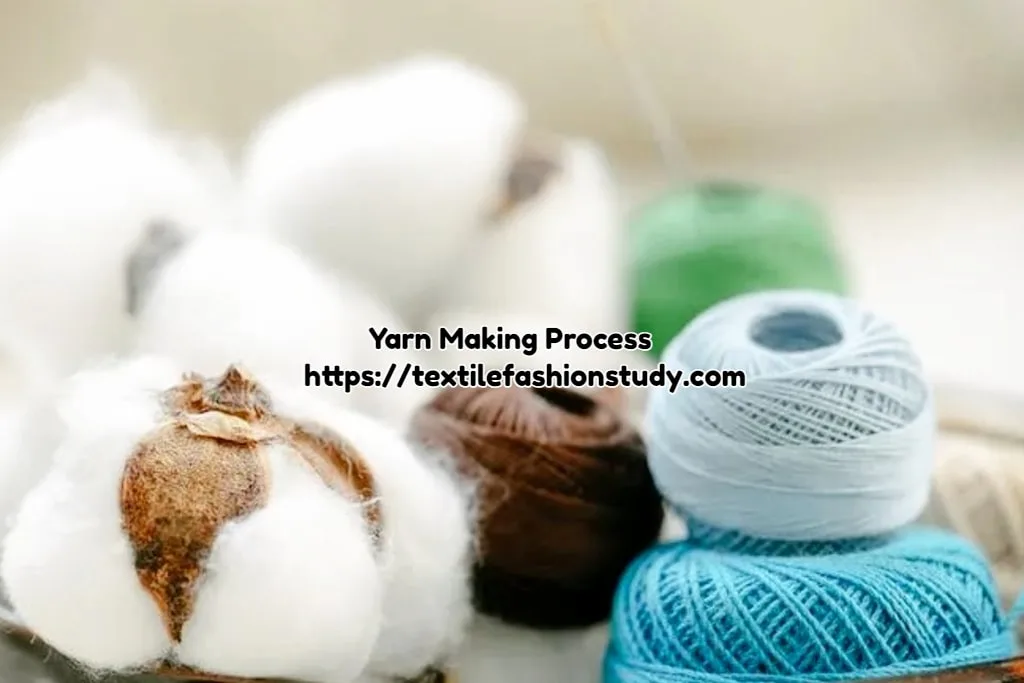
Starting a yarn trade is like a painter selecting the perfect color for their portray; it takes thought, knowledge, and a sprint of person flare. Whereas turning yarn may appear like a secretive expertise to a few, the mystery to its charm begins with choosing a fiber that talks to the yarn crafter’s heart as much as the extend at hand.
Think around the yarn’s planning application whereas selecting the perfect fiber. Will it drop like a delicate shawl over someone’s shoulders? Or will it have to withstand the happy pulling of a kid’s toy? Alpaca and silk filaments are profoundly prized in the creating world for their rich sparkle and delicate quality, which makes them culminate for clothing or extras that shout for development and shimmer. Solid filaments, on the other hand, like cotton and fleece, are incredible choices for day by day things like dishrags or sweaters since of their common sense and strength. Especially, fleece is prized for its characteristic suppleness and protection qualities, which provide each fasten a cozy hug.
Furthermore, the yarn-making enterprise depends intensely on the material sensation and the way the fiber passes between one’s fingers whereas being spun. Fine and sparkly filaments may be more fragile to work with and take time, but the result is an inconceivably indeed and smooth fasten for the craftsman. On the other hand, more grounded strands can be less difficult to work with and more pardoning. Making yarn with them more pleasant for individuals who appreciate a sensory-rich involvement.
Finally, it needs to think about the supportability and impact of fibers on the environment. Choosing fiber that is morally or locally sourced may offer a modern level of responsibility and association to the inventive process. By weaving together individual inclination, extend necessities, and moral contemplations, the culminate fiber rises from a insignificant idea to a unmistakable reality, prepared to be spun into yarn that tells a one of a kind and rousing story.
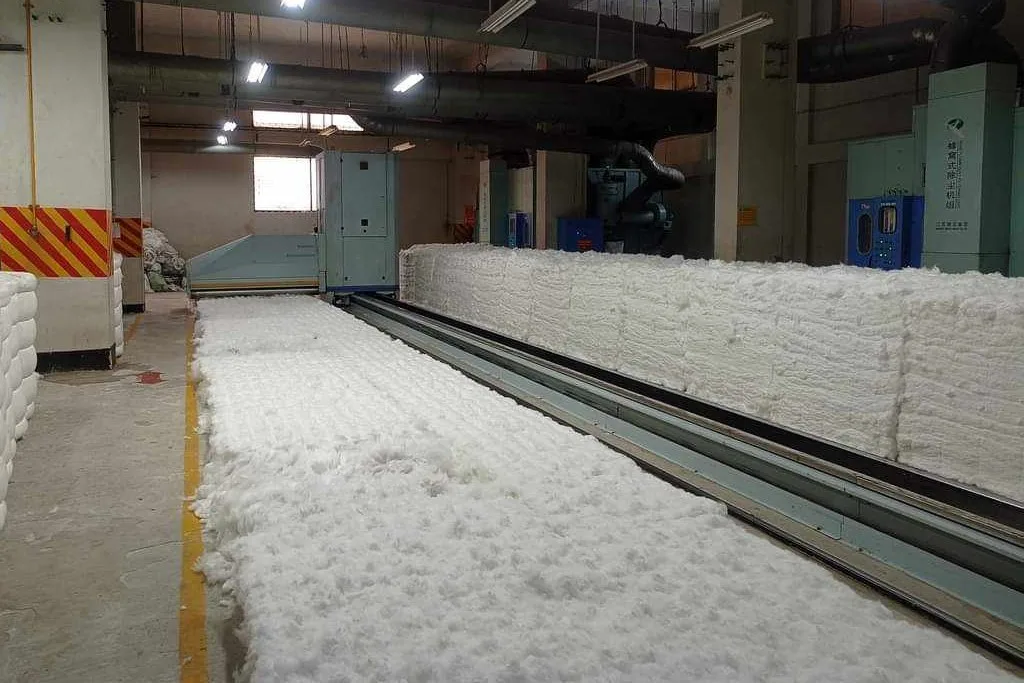
Bale Opening or Breaking
This technique opens up the cotton tufts. The first step is to release the tangled fibers because the cotton is delivered in an incredibly compacted state. The bale opener’s revolving, spiky rollers release the cotton fiber.
Mixing
This method involves combining fibers from the same or other categories to provide the required qualities at an affordable price. After studying the fundamental characteristics of the fiber, such as its staple length, tensile strength, fineness, homogeneity, etc., mixing is carried out.
Blow Room
Beaters and openers are used in this procedure to clean and open the cotton. This procedure removes some of the foreign components, such as dust particles, cotton seeds, and other contaminants. During this procedure, the cotton tufts are opened and cleaned, and the cotton lap is formed.
Carding
Carding is called the heart of spinning. The performance or quality of the yarn depends on the carding process. In this step, the raw fibers are cleaned, aligned, and blended to create a uniform web or sliver of fibers. This process helps remove impurities and align the fibers in the same direction.
Combing
To make combed yarn, you need to use combed yarn. By eliminating shorter strands and improving the alignment of the fibers, combing produces a sliver that is smoother and finer. To improve the yarn’s quality, natural fibers like cotton and wool are frequently used for this.
Drawing
Fibbers are paralleled through drafting. The Draw Frame is used to feed up to eight carded slivers, which are then stretched, straightened, and combined into a single sliver. At this point, fiber mixing is also an option.
Roving or Simplex Frame
The fibers that have been pulled and combed are then condensed into roving, a slightly twisted thread. A thicker strand, called roving, gets the fibers ready for spinning.
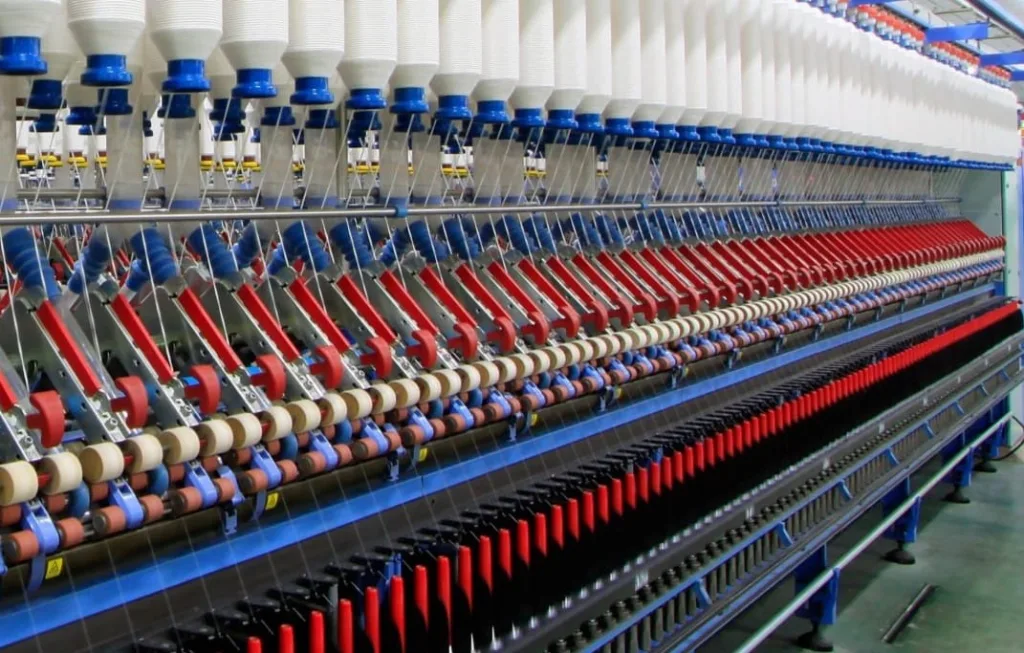
Spinning
The spinning process of spinning includes bending and pulling the wandering to deliver the wrapped up yarn. Depending on what kind of yarn you need, you can utilize ring spinning, open-end spinning, or rotor spinning to fulfill this.
The spinning forms are where the genuine enchantment happens once the fiber choice has been chosen upon. Since each turn may confer a interesting quality to the string being shaped, the fastidious move of the axle or wheel stirs the soul of the yarn. Fleece filaments that have been liberated by long-pull spinning are prepared to fill in and gotten to be a grand, lavishly delicate yarn that will make a warm winter scarf. By carefully pulling at the strands as the wheel moves, this procedure produces a yarn with bounce and exuberance that calls for a consistent, certain hand.
In differentiate, a brief draw strategy yields a yarn that is more controlled and exact, making it perfect for sensitive bind work or complicated fasten designs. The quality and delicacy required for better clothing and materials are guaranteed by the spinner’s fingers as they skillfully outline out strands, no more than an inch at a time. It’s a strategy that calls for center and tolerance, but the comes about are string that is smoother, more indeed, and loans style to each fasten it makes.
Spinning is an craftsmanship shape that includes more than basically beat and technique—it too includes assortment. Utilizing strategies like center spinning or honeycomb yarns, artisans might pick to deliver a colorfully finished craftsmanship yarn that is regularly propelled by nature’s inalienable unpredictable magnificence. These offbeat turns celebrate imperfections, spinning each skein into a one-of-a-kind work of craftsmanship with color, frame, and surface that can give identity to any handcrafted thing. These inventive turns are precisely what allow sewn or woven makes a special touch and turn them into expressive craftsmanships that communicate with the watcher without the require for words.
Plying and Twisting
Twisting
Twisting the spun yarn gives it stability and strength. The yarn’s intended purpose will determine how much twist there is.
Plying
Plying is the process of twisting two or more yarn strands together to make a stronger, thicker yarn. Plying is done for a number of purposes, including enhancing texture, boosting strength, and producing eye-catching visual effects.
After choosing the fibers for the yarn, the ply and twist of the yarn are an important but sometimes disregarded step in the yarn-making process. The number of strands that are twisted together to create the finished yarn is referred to as plying. It’s around this point that the yarn’s character really starts to take shape, so this isn’t just an afterthought. Multiply yarns give strength and consistency, resulting in a smoother, more refined finish, whereas single-ply yarns have a more rustic, homespun feel. Once incorporated into a piece, the yarn’s drape and stitch definition are affected, in addition to its longevity; therefore, it is important to twist these plies strategically.
Winding
To make handling and shipment easier, the finished yarn is coiled into cones or spools. This process also aids in getting rid of any last imperfections in the yarn.
Yarn Dyeing
Color also has a whimsical existence in the life of yarn. Dyeing methods may turn plain yarns into canvases filled with colors that contrast sharply or blend subtly. A basic design may be given a vivid, artistic touch that is reminiscent of Impressionist painting by using variegated yarns, or yarns dyed in different colors. Yarns in solid colors can give an elegant, timeless appearance that brings the stitchwork and pattern to life with unmistakable clarity. From kettles to hand-painted techniques, each skein dyeing process adds a unique story to the production, telling a different visual tale.
Adding color to a skein of yarn is like adding life to a blank canvas. The dying process is a personal dance between color and medium, where each dip and dye bath narrates a tale of artistry and creation. Dyeing is more than merely splattering colors over fabrics. The magic really happens on the path from a natural, undyed condition to a vivid, multicolored skein, transforming a plain thread into a canvas for artistic expression.
Upon dipping the yarn into the dye, an array of opportunities materialize. Without using words, color may elicit emotions, create moods, or deliver messages. Any crafter may be inspired to create gradients, speckles, or rich, saturated tones by immersing wool, silk, alpaca, or cotton into the dye baths. Layering and technique are equally as important in dyeing as color. Each yarn becomes a unique work of art when it is dyed by immersion methods, hand painting, or kettle dying. After that, heat is used to set the colors, guaranteeing that they will stay true to color wash after wash.
After it has dried, the finished item is a reflection of the dyer’s talent and vision. Seeing these yarns knitted, crocheted, or woven into clothing and embellishments is a whole creative experience. The colors used may accentuate the intricacy of a design or work well alone; solid hues lend an air of permanence, while variegated skeins use color changes to tell tales. The vibrantly colored yarn lifts every stitch, creating works of beauty that warm the body and the soul. This dyeing yarn technique skillfully demonstrates how color is not only a feature of the material but rather the fundamental soul of it.
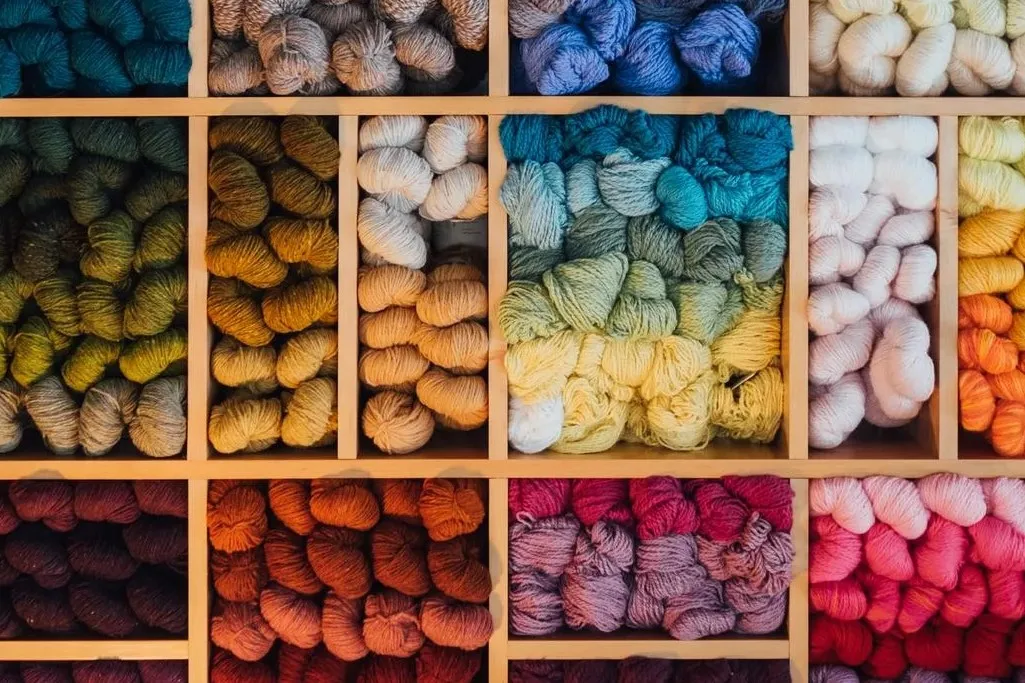
Yarn Finishing
To obtain certain qualities like delicateness, sparkle, or color quickness, the coming about yarn may go through assist methods like washing, steaming, or chemical treatments.
Penetrating is a domain where yarns serve numerous purposes, connected, and impact wrapping up and washing strategies. After it is spun, a yarn’s travel doesn’t conclusion; its surface and delicateness can be altogether affected by how it is wrapped up and cleaned. Thick, thick textures are made by strategies like fulling, which tenderly felts the filaments, and are perfect for warm winter pieces of clothing. For treasure pieces planning to final through eras, a mellow hand wash may hold a yarn’s common gloss and spring. A honest to goodness bond is made between the craftsman and their creation that is nothing brief of superb, with each turn, turn, handle, and color giving the yarn a special personality.
As a yarn craftsman, paying consideration to detail includes both celebrating the wrapped up item and being exact all through the inventive prepare. It may appear that the work is wrapped up after the filaments are chosen and spun. On the opposite, genuine enchantment happens with the fastidious application of wrapping up touches. Comparative to how a painter’s final brushstroke may take a portray from extraordinary to fabulous, so as well can yarn imagination be upgraded by these wrapping up touches. The final touches on a yarn constitute its creation’s move. These can include a wide run of techniques, but blocking and labeling stand out in particular.
Blocking is a kind of craftsmanship unto itself; it sculpts and sets the fastens, uncovering the yarn’s wealthy designs and inborn magnificence. For complicated plans like lacework, where each yarn over and knit-two-together must be shown with exact detail, this strategy is basic.
In the interim, labeling is a step that’s now and then missed, but it incorporates more than fair the fiber type—it too incorporates the level of care that goes into making anything. A exhaustive name might incorporate data on the yarn’s fiber composition, sources, and washing rules, building a relationship with the imminent creator, who will be mindful of the yarn’s travel. Indeed after the spinning wheel is quiet and the color has set, yarn making is brought to completion with a profound understanding of how indeed the scarcest alterations can upgrade the conclusion product.
Rinsing and drying the hank after hand coloring is pivotal. It ensures colorfastness and has an affect on the last immersion and tint. These strategies bring the filaments to their most extreme sign and ensure life span whereas too moving forward their stylish offer. Moreover, those who work with yarn are able to see these nuances, understanding that the charm in their generation begun long some time recently the exceptionally to begin with fasten was made. These final subtle elements lift the yarn’s imaginative quality and illustrate the otherworldly relationship between the craftsman, medium, and craft.
Every step in the exact and rich move of making yarn is carefully arranged to get the perfect result, from the fragile turn of the shaft to the final sprinkle of color. We have examined the enchantment that changes conventional strands into durable, colorful, and touch-inviting yarns in the chapters on utilizing and bending, yarn biting the dust, and yarn wrapping up. The conclusion item of these strategies is yarns that are implanted with the purposeful and enthusiasm of their makers, in expansion to the legacy of their filaments.
Yarn is a universe of perpetual conceivable outcomes, prepared to be weaved into the texture of our common social history, our lives, and our craftsmanship since of this substantial cooperative energy between maker and material.